石油基潤滑油脂之來源與製造 │ 各種石油基潤滑產品簡介 │ 合成液體潤滑油 │ 潤滑脂
石油基潤滑油脂枝來源與製造→
來源 原油的種類 原油煉製成基礎油的程序 潤滑基礎油 添加劑 摻配 包裝
一、石油基潤滑油脂之來源與製造
(一)來源
石油基潤滑油的主要來源為「原油」
(Crude oil)。
原油的生成有兩種說法,一為億萬年以前動植物埋藏於地下,受高溫高壓作用變化而成;二為在地殼深處的高溫、高壓、絕氧和金屬催化條件下,氫和碳的化合物,發生化學反應而成。
由地下挖出或抽出之原油為淺黃色至黑褐色的油狀液體。原油在大氣壓力下經過蒸餾塔蒸餾之後,可按沸點之不同而分為汽油、石油腦(Naphtha)、煤油、柴油、以及殘留於塔底之蒸餾餘油,稱之為常壓蒸餘油
(Topped crude)。
按煉油法而分,約可將石油產品分為以下各類:
- 蒸餾油(Distillate oils):在真空或低壓裝置中經氣化,再冷卻凝結而煉製的油料,均稱為蒸餾油,一般用作燃油。
- 蒸餘油(Residual oils):在真空蒸餾煉油過程中,不經氣化而殘留於塔底的成份,一般供製汽缸油、黑油之用。
- 原料油又稱基礎油(Base oil 或 Base stock):已經精煉的純淨油料,可再供摻配成中高級潤滑油的油料。
- 帶蠟蒸餾油(Wax Distillate):石蠟基原油煉得的蒸餾油中含有帶臘的油料。此種油料因流動點高,不易流動,需經脫臘後,才可製成流動性良好的潤滑基礎油。
- 汽缸油料(Cylinder Stock):適於製造汽缸油的蒸餾油。
- 亮滑油料(Bright Stock):真空殘渣油,經丙烷脫柏油後,所得脫柏油再經溶劑萃取,脫蠟及氫化精煉後所製成極高黏度亮滑油。
- 中性油(Neutral oils):真空蒸餾所得輕質,中質及重質等不同黏度油料,再經溶劑萃取,脫蠟及氫化精煉所得之輕,中及重黏度高品質油,統稱之為中性油,
其黏度約在
100 SSU 至1000 SSU/100℉之間。
- 溶劑精煉油(Solvent Refined oils):經溶劑精煉除去芳香烴,環烷烴及雜質,可提高黏度指數及氧化穩定性。
- 氫化精煉油(Catalytic Hydroprocessing oils):真空蒸餾油經氫化裂解,氫化觸媒脫臘等精煉製程所得低芳香烴,高黏度指數及淺色高品質油料。
- 紅油(Red oil):經過硫酸處理但未徹底過濾的蒸餾油或蒸餾餘油,可摻製機器油用。
- 淺色油(Pale oil):經過濾後所得顏色較淺的油。
- 深色油(Dark oils):呈黑色的蒸餾油。
- 純礦油(Straight mineral oil):不含任何添加劑的機油。
其中常壓蒸餘油經過真空蒸餾、脫瀝青、溶劑萃取精煉、脫蠟、及加氫精煉後,即成各種不同品質及黏度的基礎油(Base oil)。再以基礎油為原料,加入添加劑並摻配一定的黏度,即成為潤滑油。
(二)原油的種類
由於原油產地的不同,在外觀和性質有很大的不同,但其組成元素幾乎都是一樣的。其中有
83-87%
的碳成分、
11-14%
的氫成分、其餘的則包含有氧、氮、硫及一些金屬,如鎳、釩等。就潤滑用油立場而言,原油可按其化學組成分為下列數種:
- 石蠟基原油(Paraffinic base crude),以石蠟基之碳氫化合物為主、含蠟多、流動點高,經精煉後可製成高品質潤滑油。
- 環烷基或柏油基原油(Naphthenic or Asphaltic base crude),以環烷基之碳氫化合物為主、含蠟少、流動點低,經精煉後可製成冷凍機油,環烷基型橡膠軟化油及變壓器油,此種原油來源漸少。
- 混合基原油(Mixed base crude),含有以上
1、2
兩項之成份,既含蠟、亦含瀝青,來源最多,精煉後可得高黏度指數之高品質潤滑油。
- 芳香基原油(Aromatic base crude),含芳香基較明顯。具高度未飽和環狀碳氫化合物,反應性強,有高溶解度,高溫易氧化,黏度指數低。
(三)原油煉製成基礎油的程序
基礎油的製程有兩種方式,一種是分離
(separation)
,另一種是轉化
(conversion)
。利用分離的方式製造的基礎油稱之為傳統基礎油,而以轉化的方式所製得的油則稱為非傳統油。真空蒸餾所得的真空蒸餾油
( Vacuum distillates)
,經過這兩種方式的製程與精煉後,製造出石油基潤滑油的基礎油。基礎油的製造過程包含有五個步驟:
1)
蒸餾
2)
脫瀝青
3)
溶劑萃取或氫化精煉以改善黏度指數與品質
4)
溶劑或觸媒作用脫蠟以改善低溫特性
5)黏土或加氫精製加工以改善色澤,,穩定性等
所謂傳統的分離煉製就是以溶劑萃取、溶劑脫蠟、最終再以加氫精製加工,目前約有三分之二的石蠟基礎油是以這種方式生產。較新的非傳統轉化煉製是以氫氣在溫度、壓力、與觸媒的作用下,產生化學反應去除不需要的物質;非傳統的全氫處理過程
(All-hydrogen processing)
包括氫裂解、觸媒作用脫蠟、與加氫精製。
圖表
1
顯示傳統與非傳統基礎油煉製的兩種過程示意圖。
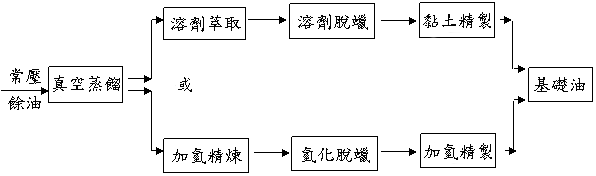
圖表1
基礎油煉製過程示意圖,分離製程(上)與轉換過程(下)
1.
真空蒸餾
( Vacuum Distillation)
原油先在常壓蒸餾下將較輕的油料取出,塔底殘餘油在溫度約達
700°F(371°C)
時將可能產生熱裂解,所以在常壓蒸餾後,將塔底殘餘油引進真空蒸餾塔內。這些較重的殘油進料,在低壓
(10mm
汞柱
)
或真空下,沸點降低所以蒸餾不會引起熱裂解的發生。真空蒸餾主要控制的性質有油的黏度、閃火點、及殘碳量。通常四至五種真空餾份,按其沸點之高低分為重柴油餾份
(Heavy diesel fraction)
、輕質餾份(Light fraction)
,中質餾份(Medium fraction),及重質餾份(
Heavy fraction
)等四種餾份及殘留於塔底的真空蒸餘油(Vacuum
tar)或稱為真空殘渣油(Vacuum
residue)即可滿足潤滑油製造的需求。供真空蒸餾或供製造潤滑油的原料,均為常壓蒸餾所得的蒸餘油,特稱為「潤滑油進料油」簡稱為「進料油」(Lube
oil feedstock or Feedstock)。
如以環烷基原油(或稱柏油基原油)為原料,真空蒸餾的各餾份中不含蠟份,或所含蠟份甚少,經精煉後即可得低流動點及較低黏度指數油料,可供冷凍機械潤滑之用。
如以石蠟基或混合基原油為原料時,各真空蒸餾餾份均含有蠟份,流動點高,且黏度指數亦高,須再經溶劑萃取及脫蠟除去蠟份後,才可得低流動點及較高黏度指數油料。此種石蠟基原油精煉所得基礎油可攙配成高品質潤滑油,供車輛及工業機械潤滑之用。
因此由真空蒸餾所得的蒸餾油及真空殘渣油都可作為煉製潤滑基礎油的進料油,其中真空殘渣油需進一步丙烷脫瀝青得到脫瀝青油,然後將所得蒸餾油及脫瀝青油再度精煉,便可製成不同黏度之輕、中、重質的中性油及高黏度亮滑油。其品質及產率深受原油特性及煉製條件影響。同時大部份潤滑基礎油均從石臘基原油煉製而成。
在傳統溶劑煉製的製程下,基礎油的黏度是由蒸餾出的餾份的黏度所決定;但在氫裂解的製程下,最終的基礎油黏度是與真空餾份的黏度是無關的,因為氫裂解的過程下,新的分子已產生。
2. 脫瀝青
( De-asphalting)
真空蒸餾的塔底殘留油,仍保有潤滑基礎油可用黏度非常高的碳氫化合物,但蒸餾已無法將殘留在內的瀝青分離,所以採用了溶劑萃取的方式脫去瀝青。常用之溶劑有丙烷、戊烷及丁烷。其中以「丙烷脫瀝青法」(Propane
deasphalting)最為有效。
脫除瀝青後之真空殘渣油,稱為「脫瀝青油」(Deasphalt
oil,簡稱DAO)去除瀝青後的殘餘油主要是包含有飽和烴和芳香烴,再經溶劑萃取芳香烴後,作為高黏度的基礎油使用,通常稱為亮滑油(brightstocks),其黏度在100°
C可超過
45 cst。另一種脫瀝青與萃取芳香烴一併進行的過程稱為是雙溶劑(Duo-Sol)精練過程。這個過程一方面脫除瀝青,一方面萃取芳香烴後成為潤滑基礎油的進料。丙烷用於脫除瀝青,酚或甲酚(cresylc
acid)則用於萃取進料。
3.
基礎油的精煉過程
(Lube Refining Proces)
以酸、溶劑與氫化精煉是幾種用於煉製基礎油所使用的過程,用以去除芳香烴與其他不需要的成分,來改善黏度指數和基礎油的品質。
A.
酸精煉
(Acid
Refining)
用酸來精煉真空蒸餾油已經不常用了,因為酸殘留物很難處理,所以現在大都已被溶劑萃取的方式所取代。有一些顏色非常輕的白油煉製或使用過的舊潤滑油的再製回收仍然使用酸精煉的方式。經與硫酸處理後,芳香烴的含量減少,使得黏度指數提高。酸精煉需複雜的中和與後續的吸附處理,以消除酸殘餘物質。
B. 溶劑萃取
(Solvent Extraction)
真空蒸餾油及脫瀝青油,因油中仍含有多量對潤滑有害之不安定之成份,不僅使油料黏度指數偏低,而且氧化穩定性低。如高分子成份、芳香族成份、聚環烷基成份(Polynaphthenes)、聚環基成份(Polycylics),或其他雜環等有害之成份,均須充份去除。以提高油料黏度指數及安定性。此一過程稱為「精煉」(Refining)。普遍使用「溶劑精煉方法」(Solvent
Refining Process)精煉潤滑油。以本法煉製時,必須選用一種對潤滑油中所含不安定之成份,如上述芳香族成份等,具有特別之溶解性,而對高品質或高黏度指數之石蠟基潤滑油具有極微之溶解者。如此經溶劑處理之後,油中所含之芳香基等不良成份大都為溶劑所萃取而除去,品質因而大為提高。
相較於酸精煉以化學反應的方式將芳香烴含量減低,溶劑萃取是以物理反應分離方式將芳香烴萃取出來,取出芳香烴的基礎油通常稱為中性油(solvent
neutrals–SN)。另一部份是溶劑與芳香烴的溶合物,將溶劑蒸發後則得到大部分的芳香烴油。其實溶劑溶合物中,視原油的不同,除芳香烴外,也可能有高達30%-50%的石蠟基油在內。目前常用之溶劑,有下列各種:
l
糠醛(Furfural)--有效溶化油中所含對潤滑有礙之各種雜質,而且其比重小,表面張力高,容易與萃取之油料分離,以利回收。
l
酚(Phenol)--效果亦佳,但須加入少許水份,以增加溶劑之選擇溶解力。唯有腐蝕性,操作應小心並做好設備防蝕。
l
丙烷與甲酚(Propane
and Cresylic Acid)混合溶劑--多用於黏度極高之油料,如汽缸油等。以本法為溶劑者,又稱為「雙溶劑精煉法」(Duo-Sol
Refining Process)。
l
二氧化硫及苯--在高壓下,以液體二氧化硫和苯作溶劑,其精煉效力亦高,但須高壓而且二氧化硫具腐蝕性,為其缺點。以本溶劑精煉者,又稱為Edeleann法。
l
N-Methyl-Pyrollidone(NMP):此種溶劑具有高度溶解力,穩定性高,操作費用低且毒性低及所產生萃餘油顏色低等優點,是最近發展出來萃取溶劑。
常用為萃取之溶劑以糠醛、酚及N-Methyl-Pyrollidone(NMP)使用最為普遍,但因酚具有腐蝕性,使用漸少。過去也以二氧化硫來使用,現今已非常少用,僅少部分的環烷基油的精煉使用它。最近一些使用糠醛或酚的煉油廠已改用NMP,因為NMP是無毒、且具高溶解度、使用量低、省能源;如設立新廠其硬體投資較省、操作費用低。如果真空蒸餾油的芳香烴或環烷基烴含量越高,則溶劑萃取的執行度越高,因而溶劑溶合物的量也越多,相對的基礎油的產量將越少。萃取物的量的多寡將影響傳統溶劑精煉的成本。溶劑萃取後的基礎油可提高VI值,熱與氧化穩定性也可以提高,一般標準溶劑萃取精煉要求基礎油的VI值需達到95,所以溶劑萃取的執行度將配合這樣的要求。基本法則是VI值欲提高一個點數,溶劑溶合物的量要多增1%。有些煉油廠僅精煉達VI值70或
80再以VI改善劑提昇VI,因此可減低15%-
20%的萃取成本,但缺點是其氧化穩定性較低,也可能含較高的硫含量或芳香烴量;以溶劑萃取法的經濟考量,真空蒸餾油的最低限定值須VI值50。必須注意的是往後的溶劑脫蠟需再取走約20%的基礎油的量,這也是為什麼在傳統溶劑萃取的製程下平均需10桶原油的量,才製成1桶潤滑基礎油的原因。
C.
加氫反應與氫裂解精煉過程
( Hydrogenation and Hydrocracking Process)
傳統的溶劑精煉法是以物理反應的分離方式去除真空蒸餾油內不需要的物質,而加氫反應與氫裂解法是以氫氣改變礦物油的分子結構的。不穩定的極性分子包含硫、氧、氮等與氫結合後被移除而變得穩定,氫裂解是加氫反應過程中最嚴苛的執行方式。嚴苛的加氫反應在高溫、高壓與觸媒的作用下使芳香烴轉化成飽和的環烷基烴與石蠟基烴。在約400°C與3000psi氫氣下,碳與碳的鍵裂開而將較大的分子分裂成較小的分子。除了芳香烴將飽和外,環烷基的環也會打開。氫裂解通常以製成
95-105 VI的基礎油為目標,更嚴苛的執行度可使VI增加至115以上,但產量會顯著減少。如以高蠟含量的石蠟基油為原料,
可達更高的VI值(
>130)。利用這些過程,潤滑基礎油的特性比起溶劑分離精煉法更容易設計與訂製。
由於氫裂解過程大都將較大,較重的分子分解成較小、較輕的分子,所以氫裂解油的黏度都較低(
80-500 SUS, ISO VG 22-100),也因此氫裂解油不單獨適用於很多重工業與引擎機油使用,除非它與溶劑煉製油或與增稠添加劑混合以增加它的黏度使用。
氫裂解的另一項優點是對於原油品質良窳的依賴度將降低。溶劑精煉的經濟效益取決於最終基礎油的生產量,而氫裂解卻可彌補原油的品質而有較高的產量,因此氫裂解製程特色有:1.它可取代傳統製程之溶劑萃取;2.它可使用低品質原油作進料;3.除去大部份含硫及含氮及含氧成份;4.可生產低芳香烴,顏色淺,高黏度指數之較高品質基礎油;5.操作費用低及產率高。
可以預見的是,將來的潤滑基礎油的煉製將會朝向加氫反應與氫裂解法來生產而逐漸取代傳統溶劑精煉的方式。氫裂解法與傳統的溶劑精煉比較有下列的優點:
1/
有較高的潤滑基礎油的產量:轉化欲移除的物質成潤滑油。
2/
生產進料較有彈性:允許較劣質與便宜的原油來生產基礎油。
3/
有較高品質的基礎油:可生產品質要求較高的的基礎油,如Group
II, III油。
4.
基礎油的脫蠟過程(Lube
Dewaxing Process)
真空塔底的脫瀝青油與真空蒸餾油經過精煉後,蠟含量仍然存在油中,這些蠟必須加以去除,使基礎油得到必要的低溫性質。溶劑脫蠟、觸媒作用的脫蠟是目前使用的方式。
A. 溶劑脫蠟(Solvent
Dewaxing)
長鍵,高熔點的蠟將影響潤滑油的低溫流動性並提高流動點,因為在低溫下蠟開始結晶,使油變得渾濁且黏度增高。
油中所含之蠟份,有結晶形蠟(Crystalline
wax)與非晶型之微晶蠟(Micro
crystalline wax)兩種。前者通稱為「石蠟」(Paraffin
wax),多存在於真空蒸餾油等餾份中;後者則多留於真空殘渣油中,且視製品之軟硬,分別稱為凡士林(Vaseline或Petrolatum)或Cersin,或微晶蠟等。
溶劑脫蠟過程包含三個步驟:晶化、過濾與溶劑回收,是較複雜且操作費用較高過程的。將石蠟油先與溶劑混合,稀釋後再降溫以使蠟結晶,然後將蠟過濾分離是傳統的脫蠟法。常用的溶劑是MEK(methyl
ethyl ketone)或丙烷(Propane),可將流動點降低至
–12 °C,如欲更低則可採用一些歐洲廠採用的Di-Me
(dichloroethane-dichloromethane
mixtures)
溶劑脫蠟。
B.
觸媒脫蠟或氫化脫蠟過程(Catalytic
Dewaxing or Hydrodewaxing)
傳統的基礎油的煉製過程中最複雜的莫過於溶劑脫蠟。除了操作成本高外,對於流動點降低的侷限也是它的缺點。現今已發展出將無支鍵的長鍵、短鍵,或支鍵少的石蠟基烴,在加氫反應(氫裂解)與觸媒作用下,使蠟的長鍵斷裂成較輕的物質,或形成支鏈異構化(isomerization)的無蠟、異構石蠟基的潤滑油分子,以此改善潤滑油的低溫特性。它較具成本效益,是溶劑脫蠟的有效取代方式。
在1979年美孚公司首先提出美孚潤滑油脫蠟過程(Mobil
Lube DeWaxing Process – MLDW),不同於溶劑脫蠟以物理分離蠟晶子,MLDW主要是將蠟在觸媒作用與加氫反應下,將蠟分裂成較小的石蠟基油與量大較輕的燃油副產品。MLDW的產能由於產生較多的輕質副產品,所以基礎油的產能較差。
此後因觸媒的發展,使得更嚴厲的氫異構化過程能夠完成(Mobil
Selective DeWaxing – MSDW),故能得到高產能的無蠟的異構石蠟基油。異構化除蠟過程(isodewaxing)可以使流動點降至
–45 °C,但需注意的是,如果此過程將流動點降得太低(視操作條件與觸媒),也會損失VI值的。現今的觸媒脫蠟技術已可生產具低流動點與高VI油,並有高產能的目標。
5.
加氫精製加工過程(Lube
oil Finishing Process)
今日,加氫精製加工過程(
Hydrofinish or hydrorefining)是溶劑萃取與脫蠟過程後最後一道加工製程。過去使用費用較高的酸處理,與以活性白土或酸性白土(Active
or Acid Clay)吸除油中所含極微量之雜質,使油脫色。此即稱為「白土過濾」(Clay
Filtering)。唯因處理後廢白土處理不易,所以白土處理法現在很少使用,而以加氫處理來取代。
加氫精製加工是一種比較輕微的加氫反應(hydrogenation),處理用以改善潤滑油的色澤、氣味,並移除表面活性物質,以加強消泡及解乳化能力。這個過程並不會如其他較嚴苛的加氫反應會使芳香烴飽和,或使碳與碳的鍵斷裂,通常也不具有除硫份的能力;但如超過100
bar的壓力下所進行的較嚴厲的氫化處理,則具相當的除硫份與解芳香烴化能力。在製造冷凍機油、變壓器油、渦輪油、白油時,有時也額外的以漂白黏土作黏吸處理,進一步濾過與去色。
6.
混合式潤滑油煉製過程(Hybrid
Lube Oil Processing)
將傳統的溶劑精煉、與嚴苛的氫化處理、及氫裂解合併一起的過程,稱之為混合式煉製過程。欲製造較高VI(>105)與較低硫份的油在溶劑精練後,則以中度嚴苛的加氫處理,取代傳統的溶劑脫蠟(如渦輪油的製造);如仍使用傳統的溶劑煉製過程,產量損失大,且硫份也無法完全去除(僅達約80%)。混合式煉製可以保持較高的產能,真空蒸餾油先經過溶劑精煉後,再加以氫處理。另一種混合式煉製的應用是將糠醛先低度萃取後,在較小型的反應爐,生產較低度氫裂解加工的裂化油;較少量的氫氣消耗搭配現有的溶劑煉製設備,可提供品質尚優,生產經濟效益較佳的油。
7. 蠟異構化過程(ax
Isomerization)
七十年代初VHVI油已可經由蠟煉製,而蠟是由溶劑脫蠟而得。長鍵的正石蠟基或支鍵少的石蠟基,在觸媒作用下氫裂解過程與異構化轉化成異構體後,可製得具良好的低溫特性與高VI油。將蠟異構化是製造超高VI(>140)基礎油的過程,這個過程的次序是先經過氫裂解後,再續以氫異構反應。由於進料的蠟已是無芳香基與無環烷基的原料,所以觸媒作用可以極佳化的轉化這些石蠟物質,過程中產能損失較大,但可以生產出高品質價格較高的裂解油(
Shell XHVI, Mobil MWI, Exxon Exxyn)。
圖表2
顯示經由氫裂解與蠟異構化,包括溶劑脫蠟的過程製造XHVI油。
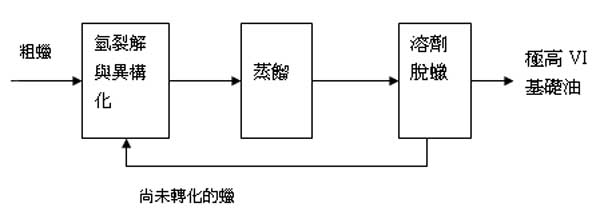
圖表2
製造極高VI基礎油過程示意圖
8. 氫開始(Hystart)
較劣質的真空餾份在尚未溶劑萃取前可先以氫化處理以提昇它的品質,這個過程稱之為氫開始(Hy-starting
or Hystart)。
9.
全氫過程或路徑(
All-Hydrogen Process or Route)
基礎油的生產過程中以氫裂解,觸媒反應無溶劑脫蠟,加氫精製加工的過程稱之為全氫過程或路徑,視氫裂解的執行嚴峻度可製得HVI油與VHVI油。
10.
不同氫化處理基礎油與溶劑精煉油之比較
基礎油類型
(Base
stock type) |
加氫精製(Hydrofinished) |
加氫處理(Hydrotreated
VHQ) |
加氫裂解
(Hydrocracked
HDC, VHVI or XHQ) |
溶劑精煉
(Solvent-refined) |
氫化執行度 |
低 |
中度 |
高 |
- |
氫化處理目的 |
飽和烯烴與芳香烴,移除硫與氮 |
飽和烯烴與芳香烴,移除硫與氮 |
飽和烯烴與芳香烴,移除硫與氮,打開環狀結構 |
- |
進料 |
經溶劑精煉 |
經溶劑精煉 |
真空蒸餾:HDC與
VHVI;真空蒸餾,粗蠟:XHQ |
- |
性質檢驗 |
與進料微小改變 |
較低芳香烴,硫與氮 |
極低芳香烴,硫與氮 |
- |
黏度指數(VI) |
90 - 105 |
105+ |
95 – 105 (HDC)
115 – 130(VHVI)
130+ (XHQ) |
90 - 105 |
ISO黏度範圍 |
22 - 460 |
22 – 100 |
22 –100 (HDC/VHVI)
22 –46(XHQ) |
22 - 460 |
改善性能元素 |
改善色澤,解乳化性、消泡性 |
改善氧化穩定性 |
氧化穩定性大幅提昇 |
- |
溶解性 |
極優 |
良好 |
中度 |
極優 |
(四)潤滑基礎油
原油經常壓、真空減壓蒸餾所得潤滑油餾份,經溶劑精製,溶劑脫臘及白土或加氫精製而成潤滑基礎油。潤滑基礎油之成份,以碳與氫之化合物(Hydrocarbon
Compounds)之混合物為主,約佔99%以上,其餘為硫、氮、氧等之化合物。黏度低者,其分子量約在250以上,高黏度者,其分子量超過1,000。
由於原油中碳與氫化合物分子結構形成之不同,而分有:
石蠟基油(Paraffinic
base oils或Paraffinic
oils)
環烷基油(Naphthenic
base oils或Naphthenic
oils)
芳香基油(Aromatic
base oils或Aromatic
oils)
混合基油(Mixed
base oils)
如與環烷基及芳香基油比較,石蠟基油之比重較小,流動點與閃火點均較高,且有最佳之抗氧化特性,經久耐用;其黏度受溫度之改變亦較小,即黏度指數較高,故作潤滑基礎油用者,以石蠟基油為最佳。
如以SAE
30號之石蠟基與環烷基油為例,可比較如圖表3。早期以美國賓州(Pennsylvania)所產之原油屬石蠟基油,經過簡單提煉,即可製成品質良好之潤滑油。過去都認為賓州原油煉製之潤滑油為最佳。如今,由於煉油技術之不斷進步,且新油源相繼開發,可由任何一種原油煉成高黏度指數之石蠟基潤滑油,且其品質更駕賓州潤滑油之上。
圖表3.石蠟基與環烷基油之比較
SAE 30
性 狀 |
石蠟基 |
環烷基油 |
黏度 |
|
|
SSU/210℉
|
61 |
61 |
SSU/100℉
|
460 |
650 |
cSt/210℉
|
10.5 |
10.5 |
cSt/100℉
|
99.3 |
140 |
比重,Sp.Gr.60/60 ℉
|
0.886 |
0.905 |
閃火點,℉ |
490 |
430 |
流動點,℉ |
+5 |
-30 |
黏度指數 |
96 |
20 |
抗氧化性 |
1,500 |
1,000 |
揮發性 |
較小 |
較大 |
環烷基油之特點為流動點特低,主供冷凍機等需要低流動點機件之潤滑。
在國際上基礎油買賣,除指明為何種基礎成分(如石臘基或環烷基)外,主要是以粘度作為分類,其分類編號表列如圖表4。
在台灣煉製潤滑基礎油的公司只有中殼潤滑油股份有限公司一家,這家公司是由中國石油與殼牌公司合資的公司,煉廠在高雄市郊,生產的基礎油除供台灣地區自用外,也有部分外銷各地,產品的編號及規格簡述如圖表6。
中國大陸的中石油及中石化所屬煉油廠,也煉製大量基礎油,主要為國產原油經常減壓蒸餾,再經溶劑精製,溶劑脫臘及白土或加氫精製而成。其產品除供國內外使用之外,同樣有部分外銷,出口標準見圖表6-1。
基礎油之品質主要以具有高粘度指數、低含硫量、酸值小為主要特點。經過溶劑萃取之後的油,一般粘度指數在90-100之間,若改採深度加氫處理,所製成之基礎油粘度指數可達到100以上,而且此種程序處理時,不用選擇特定種類的原油。此類基礎油中,低粘度指數的成份已被除去,分子重量也轉化為較輕的組成,因此,可以提高輕質(低粘度如SAE
5W/30)油的產出量,目前市場正成長中。
API潤滑基礎油分類
早期潤滑基礎油並無任何分類標準,近年來由於非傳統基礎油使用日漸增多,於是1993年美國石油學會(American
Petroleum Institute,
API)為使車用機油使用基礎油之品質有所依循,因此制訂了API
Base Oil Interchangeability Guidelines,詳如圖表7,區分傳統、非傳統、合成油與其他基礎油,將潤滑基礎油分成Group
I, II, III, IV, V五大類;其中Group
I, II, III是礦物油而依其含硫量、飽和烴(Saturates)、黏度指數來分類;Group
I是傳統溶劑精煉出來的基礎油,Group
II是氫裂解製程所煉出來基礎油,Group
III則是氫裂解過程與臘油異構化製程所煉出來基礎油,Group
IV是PAO合成基礎油,Group
V是酯類及其他不包含在Group
I-IV的合成油。
傳統基礎油是使用溶劑精煉出來的基礎油,而非傳統則指包括氫化裂解油、臘油異構化油、PAO及其他類合成油。非傳統基礎油品質之特點是擁有極高黏度指數,其值約在100-130,比傳統基礎油95者為高。除此之外,飽合烴(Saturates)約在95wt%以上,不含或含極少量芳香烴,含極微量硫及氮化合物,同時揮發度較低,具良好低溫黏度特性。這些優異特性是傳統基礎油所欠缺,更是發展高品質潤滑油品所需要者。
API基礎油的分類是按基礎油的特性來區分,而不是以所使用的提煉過程來區分的。Group
I的基礎油並不一定就優於或劣於Group
II的基礎油,雖然Group
II的基礎油有較低的硫含量與芳香烴,及可能較高的VI值與氧化穩定性,但可能它的添加劑的溶解性不如傳統溶劑精煉的Group
I基礎油,基礎油是否適合調配成潤滑油,是以最終潤滑油的性能表現來衡量的。
圖表4.基礎油粘度分類表
基礎油 (BASE STOCKS)
|
大約黏度 (Approximate Viscosity)
|
|
中性油 (NEUTRALS)
|
黏度級數 |
40℃ |
100℃ |
cSt |
SUS |
cSt |
SUS |
70N |
13.3 |
70.8 |
3.00 |
37.0 |
80N |
15.6 |
80.3 |
3.35 |
37.3 |
90N |
18.0 |
89.0 |
3.4 |
37.5 |
100N |
21.5 |
104.0 |
4.0 |
39.0 |
140N |
30.7 |
144.0 |
4.5 |
41.0 |
150N |
31.6 |
148.0 |
4.9 |
42.4 |
160N |
33.7 |
158.0 |
5.2 |
43.3 |
170N |
34.0 |
159.0 |
5.4 |
44.0 |
180N |
38.5 |
181.0 |
5.7 |
44.9 |
200N |
44.5 |
204.0 |
6.2 |
46.0 |
250N |
56.1 |
257.0 |
6.5 |
47.0 |
300N |
61.3 |
285.0 |
7.0 |
49.0 |
315N |
70.0 |
315.0 |
7.9 |
52.0 |
330N |
70.9 |
328.0 |
8.4 |
53.7 |
350N |
76.0 |
358.0 |
8.8 |
55.0 |
400N |
86.0 |
398.6 |
9.8 |
58.0 |
450N |
98.0 |
454.0 |
10.5 |
61.0 |
500N |
107.0 |
496.0 |
11.0 |
64.0 |
600N |
130.4 |
604.0 |
12.1 |
66.0 |
650N |
141.0 |
665.0 |
13.8 |
71.0 |
700N |
151.0 |
698.0 |
14.0 |
73.0 |
圖表5.亮滑油粘度分類表
|
亮滑油 (Bright Stocks)
|
黏度級數 |
40℃ % |
100℃ |
|
cSt
|
SUS
|
cSt
|
SUS
|
135 Brt |
413.2
|
1875.0
|
28.6
|
135.0
|
145 Brt |
523.3
|
2425.0
|
30.9
|
145.0
|
150 Brt |
568.0
|
2632.0
|
33.0
|
155.0
|
160 Brt |
600.0
|
2800.0
|
35.2
|
166.0
|
175 Brt |
654.7
|
3034.0
|
36.0
|
169.7
|
185 Brt |
616.0
|
2855.0
|
37.6
|
177.0
|
225 Brt |
1030.0
|
4800.0
|
49.3
|
229.0
|
圖表6.中殼潤滑油公司產品牌號及規格
項目 |
品質規格(TYPICAL)
|
試驗 方法 |
70P |
LN |
150SN |
M.N |
500SN |
H.N |
150BS |
200BS |
ASTM |
ISO |
外觀 |
透明 |
透明 |
透明 |
透明 |
透明 |
透明 |
透明 |
透明 |
|
色度,號 最大 |
L1.0 |
L0.5 |
0.5 |
L1.0 |
L1.5 |
1.5 |
4.0 |
4.5 |
|
運動黏度,mm2/S
40℃
100℃
|
14.89
-
|
22.92
-
|
29.96
-
|
45.83
-
|
98.6
-
|
125.9
-
|
483
-
|
745
-
|
|
黏度指數 最小 |
84 |
98 |
98 |
99 |
95 |
95 |
96 |
97 |
|
閃點(開口),℃ 最低 |
172 |
202 |
210 |
235 |
257 |
271 |
318 |
335 |
|
傾點,℃ 最高 |
-12 |
-11 |
-15 |
-15 |
-15 |
-15 |
-12 |
-18 |
|
酸值,mgKOH/g 最大 |
< 0.03
|
< 0.03
|
< 0.03
|
< 0.03
|
< 0.03
|
< 0.03
|
< 0.03
|
< 0.03
|
|
殘炭,﹪(m)
|
0.06 |
0.06 |
0.06 |
0.06 |
0.10 |
0.11 |
0.43 |
0.52 |
|
密度(20℃),kg/m3
|
|
|
|
|
|
|
|
|
|
苯胺點,℃ |
|
|
|
|
|
|
|
|
|
硫,﹪(m) |
|
|
|
|
|
|
|
|
|
圖表6-1.中國石化總公司基礎油出口標準
項目 |
品質規格 |
試驗方法 |
75SN |
100SN |
150SN |
200SN |
350SN |
500SN |
650SN |
150BS |
ASTM |
ISO |
GB/T |
外觀 |
透明 |
透明 |
透明 |
透明 |
透明 |
透明 |
透明 |
透明 |
|
|
目測 |
色度,號 最大 |
0.5 |
1.0 |
1.5 |
2.0 |
3.0 |
4.0 |
5.0 |
6.0 |
D1500 |
2049 |
|
運動黏度,mm2/S
40℃
100℃ |
13-15
實測 |
18-20
實測 |
28-32
實測 |
38-42
實測 |
65-72
實測 |
95-107
實測 |
20-135
實測 |
實測
30-33
|
D455 |
3104 |
265-88 |
黏度指數 最小 |
100 |
98 |
98 |
96 |
95 |
95 |
95 |
95 |
D2270 |
2909 |
1995-88
|
閃點(開口),℃ 最低 |
175 |
185 |
200 |
210 |
220 |
235 |
255 |
290 |
D92 |
2592 |
3536-83
|
傾點,℃最高 |
-12 |
-12 |
-9 |
-9 |
-9 |
-9 |
-9 |
-9 |
D97 |
3016 |
3535-83
|
酸值,mgKOH/g 最大
|
0.02 |
0.02 |
0.02 |
0.02 |
0.03 |
0.03 |
0.03 |
0.03 |
D974 |
DIS
6618
|
264-83 |
殘炭,﹪(m) |
- |
- |
- |
- |
0.10 |
0.15 |
0.25 |
0.70 |
D189 |
6615 |
268-87 |
密度(20℃),kg/m3
|
實測 |
實測 |
實測 |
實測 |
實測 |
實測 |
實測 |
實測 |
D1298 |
3675 |
1884-83和
1885-83
|
苯胺點,℃ |
實測 |
實測 |
實測 |
實測 |
實測 |
實測 |
實測 |
實測 |
D611 |
2977 |
262-88 |
硫,﹪(m) |
實測 |
實測 |
實測 |
實測 |
實測 |
實測 |
實測 |
實測 |
D1552 |
|
387-90 |
圖表7.API 潤滑基礎油品質分類
分 類 |
硫份(wt%) |
飽合烴(Saturates),wt% |
黏度指數,VI |
Group I
|
> 0.03
|
< 90
|
80-120 |
Group II
|
< 0.03
|
> 90
|
80-120 |
Group III
|
< 0.03
|
> 90
|
> 120
|
Group IV
|
---------Poly-Alpha-Olefin, PAO----------------------------------
|
Group V
|
--------不含PAO外其他類合成油----------------------------------
|
(五).添加劑
潤滑基礎油不管是礦物油或合成油,如不利用現今添加劑技術,仍無法滿足高性能潤滑油的要求。
添加劑是化學複合物質,可以改善很多潤滑油的性能,他們可以加強已有的性能,抑制不想要的性能,產生變化的發生速率,同時可以加入基礎油新的有用的性能。添加劑最初在1920年代開始使用後,它的使用即迅速的增加,現今每一種潤滑油幾乎都含至少一種添加劑在內,有些含多種不同種類的添加劑,其含量可由幾百分之一的%至30%。
添加劑雖然對油的性能表現有所助益,但如用量過多或添加劑間會彼此反應,也是有害的。所以均衡的添加劑配方並經測試,確認無不良的副作用是很重要的,一旦達成有效的均衡配方後,使用者額外添加外來補充品通常是不需要的。添加劑可以按下列的功能分成兩大類:
1/
影響基礎油的物理與化學性能:物理性能如黏溫特性、解乳化性、低溫特性等。化學性能如氧化穩定性。
2/
影響與金屬表面的物理化學性:如減少磨擦
、增加極壓表現、防磨損與抗腐蝕等。
添加劑雖然對於潤滑油有很大的影響,但有些性能是不受影響的,如揮發性、熱穩定性、熱傳導性、消泡性、被壓縮性、與沸點等,優良品質的基礎油加上均衡與極佳化的添加劑組合,才能調配出高性能的潤滑油。也因此,現今有使用氫裂解與高度氫處理的高精煉基礎油,及酯類與PAO的合成基礎油越來越多。
抗氧化劑(Oxidation
Inhibitors)
當油溫度在有氧存在的情況下升高時,氧化就會發生,氧化的結果是黏度與有機酸的濃度會增加。清漆(varnish)與膠漆(lacquer)的積垢物會在高溫的金屬面上形成,更進一步的氧化下,會形成堅硬的碳類物質。
典型油老化的結果是顏色變深並有焦味,如繼續使用,油的黏度明顯的增加,也會產生酸性的氧化物質,會有腐蝕的問題。油氧化的速率受幾個因素影響,當油溫增加時,氧化速率成指數倍增。一般常理是礦物油溫每增加18°F(10
°C),油氧化的速率增加一倍;如讓油大量暴露於空氣或將空氣攪入油中,油氧化的速率也會增加。有些金屬,特別是銅與鐵,及有機酸與礦物酸類,都具有催化與促進油氧化的作用。油氧化一般是油中的自由基與氧結合,所以如能阻止這種反應,即可達到抑制氧化的效果。
抗氧化劑有兩種:一種是與自由基反應成較不活性的物質,一種是分解那些具自由基的物質,成為較不活性的化合物。當油溫低於200°F(93°C)時,
氧化的速率較慢,第一種抗氧化劑是有效的;但當油溫高於200°F(93°C)時,金屬的氧化催化效果是油氧化的重要的因素,在這種情況下,抗氧化劑的使用即應抑制或減少金屬催化的作用,這些抗氧化劑通常會與金屬表面形成一層保護膜,因此這類的物質也可稱為金屬惰化劑。常用的抗氧化劑是二硫磷酸鋅(Zinc
Dithiophosphate),它一方面具金屬惰化,一方面油溫高於200°F(93°C)時,也具分解那些具自由基的物質成為較不活性的化合物。
抗氧化劑在油高度暴露於空氣下,並不能完全防止油的氧化,只是油氧化的速率與程度較緩,所以抗氧化劑並不是萬靈丹。良好煉製的基礎油調配適合的抗氧化劑,可達到理想的抗氧化效果,氫裂解基礎油(API
group II & III)與合成基礎油如PAOs(API
group IV),也同樣需調配均衡的抗氧化劑,以達到良好的抗氧化效果。
黏度指數增進劑(VI
Improver)
潤滑油的基本性能是黏度,運動黏度會受溫度與壓力而改變,黏度指數是油在40°C與100°C的黏度的變化率,視原油的來源與傳統煉製的基礎油,其VI在80與120
之間,傳統油大都在100左右,黏度指數增進劑的使用可以增加潤滑油的黏度指數。黏度指數增進劑是一種長鍵、高分子的聚合體,它的功用是在高溫下令油保持適度的黏度,這是由於在高溫下聚合體的物理型態改變的結果。
低溫時聚合體的結構是捲曲的,而在高溫時聚合體則伸展成長線型,它彌補了油在高溫時降低的黏度。黏度指數增進劑的長鍵高分子會受機械剪力而受到影響,在中度的剪力作用下會使聚合體暫時分離,致使黏度暫時降低;當這剪力移除後聚合體恢復原型,而黏度也恢復。如高分子受機械剪力破壞後,則即使剪力移除後,聚合體也無法復元,而降低的黏度也無法恢復。
黏度指數增進劑用於汽車引擎機油、自動排檔油、多功能拖曳油、車用齒輪油、及液壓油,由於黏度指數增進劑的使用,使得潤滑油使用的溫度範圍比單純的礦物油更為寬廣。
流動點降低劑(Pour
Point Depressants)
流動點降低劑是一種高分子聚合體,其功用是在低溫下抑制蠟的形成,以避免影響低溫的流動性能。它並不能完全避免蠟的形成,但可降低形成的溫度;流動點降低劑通常可使流動點降低20-30°F(11
-17°C),但視油的不同,也可以降低達50°F(28°C)。
清淨劑與分散劑(Detergents
and Dispersants)
在內燃引擎機的運作下會產生有很多使油劣化的有害積垢物質,這些積垢物質會影響油的循環,堆積在活塞環上使活塞環卡死,導致快速的磨損。一般積垢形成後,除非是引擎拆開來排除掉,否則是很難把它移除的;使用清淨劑與分散劑,將延後積垢物的形成與堆積的速率。正常週期的換油,將污染物與未形成或堆積前的積垢排除掉。
清淨劑是化學物質,能中和因高溫形成垢物,或因燃燒含硫量較高的燃料油所形成的副產品;而分散劑也是化學物質,但相反的是它將低溫操作下所形成的油泥與膠漆,或將滲入未完全燃燒的燃油驅散,並使其懸浮在油中,懸浮在油中的污染物也可以因正常週期的換油而排除掉。嚴格的說,清淨劑與分散劑並沒有明顯的分際,因為清淨劑也具有驅散並懸浮污染物,而分散劑也具有防止高溫積垢物形成的能力。
今日所使用的清淨劑主要是有機皂與鹼土金屬鹽類,如鋇、鈣與鎂。這些有機金屬化合物具中和酸性能力,但這些有機金屬化合物在燃燒時會有灰份的殘餘物,這些灰份有時會在燃燒室內形成有害的積垢,但也能附著於排氣閥門與座上,形成抗磨的一層薄瞙。
而相對於清淨劑含金屬成分,分散劑是不含金屬成分的,所以是無灰分散劑。通常分散劑是由碳氫高分子聚合物衍生得來;最常用的是以聚丁烯為原料製得,它一方面可溶於油,一方面具活性可吸引、並包覆可能形成積垢的物質,使其懸浮於油中。
清淨劑與分散劑主要是適用於車用引擎機油內,但也使用於自動排檔油、液壓油、與高溫適用的循環機油內;在這些應用上,是防止因氧化結果產生的亮光漆,與膠漆的附著與沉澱,輔助抗氧化劑的效能。
抗磨損添加劑(Antiwear
Additives)
抗磨損添加劑使用於多種潤滑油,主要的用途是當金屬面間有相互接觸的邊際潤滑的情況下,能減少磨擦、減低磨損、刮蝕與磨紋。當油溫或負苛增加時,油膜的厚度減小,致使金屬表面開始相互接觸,當接觸面觸碰時摩擦增加,接觸點會發生熔接現象,當繼續滑動時,熔接點立刻被破壞,於是造成金屬面更粗燥,也產生磨損微粒,這些微粒也將導致金屬面的刮蝕與磨紋。
視要求的不同,有兩種物質可防止金屬間的接觸:輕微抗磨與減磨添加劑也稱為邊際潤滑添加劑,他們是極性物質,如脂肪油、酸類、酯類。因他們是長鍵物質,會形成吸附的薄膜,而其極性端點會與金屬依附一起。由於這一層薄膜,致使摩擦減少,磨損也因而降低,但在較嚴苛的情況下,薄膜會被磨掉故而抗磨效果降低。
極壓添加劑(Extreme
Pressure Additives)
在高溫或重負苛時,滑動面間有更嚴厲的情況下,則需要有極壓添加劑以幫忙減少摩擦、降低磨損,以避免嚴重的金屬表面的破壞。極壓添加劑比抗磨損添加劑更具活性,它與金屬接觸面產生化學反應,而形成一個保護膜,化學反應會隨金屬接觸產生的溫度高低而變化。即使含有極壓添加劑,初期新的金屬面的磨損仍高,但隨正常的磨合一過,則會形成保護膜;保護膜如被磨破,也能即時因化學反應而修補,金屬間的磨損可大為降低,也因此添加劑會漸漸的消耗掉,這也是適時添加新油、或定期更換油料是必要的。
極壓添加劑含有硫、磷、氯,他們可單獨存在也可能混合一起。含硫的化合物,有時也包含磷與氯,用於金屬切削油;硫磷混合物用於車用與工業用齒輪油,而最有名的硫磷化合物是二烷基二硫化磷酸鋅(zinc
dialkyldithiophosphates-ZDDP),它除具優越的抗磨損與極壓效果外,也具良好的抗氧化能力,故是現今被廣泛使用,而又具經濟效益的添加劑。
磨擦調整劑(Friction
Modifiers)
在滑動速度較低的潤滑部位,如負荷逐漸增加,或低黏度油在溫度逐漸增高的情況下,油膜的厚度不足時,金屬面間會產生顫抖滑動(stick-slip)的震動與噪音的現象。為了避免這種現象,則需加入磨擦調整劑以減少摩擦力。
磨擦調整劑的工作溫度是低於抗磨損與極壓添加劑發生反應的溫度,它含有極性油溶性物質,在金屬面形成一層薄膜以減低磨擦。它可視為較輕微的抗磨損或極壓添加劑,磨擦調整劑可分成固態如二硫化鉬、石墨等,液態如脂肪酸酯類、醚類、醇類等,它的應用在於現今節能型潤滑油、滑道油、自動排檔油等。
防銹與抗腐蝕添加劑(Rust
and Corrosion Inhibitors)
在潤滑系統中會產生不同種類的腐蝕性物質,其中兩種最重要的來源,一是來自於潤滑油本身的有機酸如熱與氧化的分解物,另一種則來自於油的污染物質。
幾乎每種潤滑油都會使用抗腐蝕添加劑,它的功能是在金屬表面形成一層保護膜,以防止腐蝕物質與金屬直接接觸。在汽油或柴油引擎中有一些燃料油中的物質如硫份、抗爆劑,經過燃燒會產生強酸,這些強酸可附著在汽缸壁,或經由潤滑油被帶到引擎的其他部位。這些酸使活塞環與汽缸壁產生腐蝕性磨損,而曲軸、搖臂等其他部位也都可能產生腐蝕性磨損。油中如含有高鹼性物質,將可以中和這些強酸。這些鹼性物質也使用於清淨劑。
使用防銹劑一般是一種高極性化合物可吸附在金屬表面,經由物理或化學反應,防銹劑在金屬表面上形成一層薄膜,防止金屬與水直接接觸。防銹劑在大部分的潤滑油中均使用,但使用時需避免一些問題;諸如對於非鐵金屬產生腐蝕性,或與水產生惱人的乳化物等,防銹劑因吸附在金屬表面,所以隨使用時間的延長會漸漸消耗掉。
消泡劑(Deformants)
潤滑油中起泡沫是非常惱人的,因為密集的氣泡將會加強氧化作用,有可能發生油抽空的損害,也可能在循環系統導致輸油不足的情況。潤滑油抵抗泡沫形成的能力通常與原油的種類、基礎油煉製的方式與程度、以及黏度有關,在很多種油的使用情況,由於攪拌的關係會引起泡沫,所以消泡劑的使用在這些情況下是有必要的。
消泡劑具較基礎油低的表面張力,它的顆粒會將小泡沫吸引而匯聚成較大的泡沫,使它易於在油面上破裂而釋放出空氣。矽類高分子聚合體以幾個ppm加入油中是最廣泛使用的消泡劑,有時候以有機聚合體來使用,但使用的濃度要高些。
油起泡沫可分成兩方面,一是表面起泡,通常可以以消泡劑來控制;另一種是油內部的泡沫,不幸的是內部的泡沫不易經由消泡劑來改善,而對表面泡沫有效的消泡劑反可能使油內部泡沫更趨穩定。對於需極佳消泡性能的油,如渦輪油,則需特選的基礎油與添加劑加以調配。
解乳化劑(Demulsifiers)
大部分的工業循環系統用油,如液壓油、齒輪油、渦輪油、與壓縮機油等,多需要良好或優良的解乳化的特性,以分離污染於油中的水。油中如果沒有解乳化劑,水在油中會產生穩定的乳化液,基本上表面活性的物質都適合當解乳化劑。現今特殊的聚(乙烯乙二醇)及其他類的環氧物質已被證實非常有效,已成為常用的一種消泡劑。
乳化劑(Emulsifiers)
乳化劑通常是使用於水溶性的金屬加工液內,它可降低界面張力,讓水與油形成較穩定的乳化液。
著色劑(Dyes)
為因應行銷或辨識與偵測漏油的目的,,有些潤滑油會含著色劑。它是以國際顏色指數來分類,通常它是以固體微粒懸浮於油中。
總括上述常用添加劑之種類、效用、化學成份、及有效添加量如圖表8;中國大陸石油添加劑分類如圖表9所示,列出供參考。
圖表8.常用添加劑
種類 |
效
用 |
化
學
成
分 |
有效添加量 |
流動點降低劑 |
具有將石蠟結晶表面包含起來之界面作用防止石蠟之連續凝集,使低溫流動性良好。寒冷地用潤滑油多有添加 |
(1)
荼與石蠟之縮合物
(2)
酚與石蠟之縮合物
(3)
甲基丙烯酸酯聚合物 |
0.1~1﹪ |
黏度指數增進劑 |
高分子聚合物,低溫時呈盤捲鏈狀構造,高溫時分子可延伸,阻礙油之流動。對低黏度油使用較有效 |
(1)
聚異丁烯系
(2)
聚丙烯酸甲酯系 |
2~10
﹪
|
消泡劑 |
添加於各種潤滑油中,可使泡沫之表面張力造成不平衡而破壞 |
(1)
矽酮系
(2)
脂肪酸酯類
(3)
醯胺系 |
2~5ppm
|
抗氧化劑 |
防止潤滑油因氧化產生酸性物質與油泥而劣化。令氧化生成之過氧化物不起連鎖反應,藉而防止氧化物之生成。另可妨害金屬之觸媒作用,間接達到抑制氧化之目的 |
(1)
酚系
(2)
胺系
(3)
有機硫化物
(4)
有機磷化合物
(5)
有機硫一磷化合物
(6)
二烷基二硫磷酸鋅 |
0.4~2﹪ |
腐蝕防止劑 |
防止軸承等金屬之腐蝕,並在金屬表面形成保護膜,防止金屬之觸媒作用,藉而防止潤滑油之劣化。 |
(1)
二硫代磷酸鋅
(2)
二硫氨基甲酸金屬鹽
(3)
硫-磷系化合物 |
0.4~2﹪ |
清淨分散劑 |
吸著使用中發生之油泥、積碳、並將之分散於油中(分散作用)。在固體表面形成吸著膜,防止碳粒、樹脂沉積於引擎內部(清淨作用)。中和因油劣化產生之酸性物質及燃料中之硫份所形成之硫酸(中和作用)。
|
(1)
油溶性有機金屬鹽(金屬為Ca,Ba,Mg)磺酸鹽、酚酸鹽磷酸鹽。
(2)
無灰份清淨分散劑(Ashless型),為不含金屬之高分子聚合物,如丙烯酸酯系。 |
2~10﹪ |
油性向上劑
(油性劑) |
油性向上劑之分子可吸著於金屬表面,或與金屬表面上之金屬氧化物發生化學反應生成皂類之吸著膜,防止金屬間之直接接觸,達到減磨目的。高溫狀態及嚴酷條件下不能使用。 |
(1)
高級直鏈脂肪酸
(2)
高級直鏈脂肪酸脂類
(3)
金屬皂類(如鉛皂)
(4)
直鏈醇 |
0.1~1﹪ |
極壓添加劑
(EP劑) |
使用於油性向上劑無效或嚴酷條件下,能與金屬表面反應形成耐膠執、耐壓性金屬化合物,防止膠執點與磨耗。E.P
劑與金屬表面反應生成低熔點化合物,為剪應力小之無機膜層。 |
(1)
有機氯化物
(2)
有機硫化物
(3)
有機磷化物
(4) Zn.二烷基二硫化磺酸鹽(極壓劑多為S-C1系,S-P系,
S-C1-P-Zn系等之混合物)。 |
5~10﹪ |
防銹劑 |
使用於多種潤滑油中。能於金屬表面形成被膜,防範水分、鹽分之侵襲,達到防止生銹之目的。 |
(1)
脂肪酸皂類
(2)
環烷酸皂類
(3)
磺酸鹽
(4)
磷酸酯
(5)
有機胺類
(6)
硫代磷酸鹽
(7)
環己胺之亞硝酸鹽(氣相防銹劑) |
0.1~1﹪ |
黏著劑 |
滑動面專用油等要求黏著性之場合使用。 |
(1)
不飽和脂肪酸之鋁皂
(2)
特殊高分子聚合物 |
|
乳化劑 |
供乳化油使用。
|
(1)
環烷酸鹽
(2)
脂肪酸皂類 |
|
著色劑
|
賦予特定呈色或螢光,與潤滑油之性能無關。 |
油溶性染色等 |
|
除以上較常用的添加劑外,尚有下列較特殊具特定用途的添加劑:
(1)脂肪油(Fatty
Oils)。
(2)增稠劑(Thickening
Agents)。
(3)矯臭劑(Odor-Control
Agents)。
(4)顏色安定劑(Color
Stabilizers)。
(5)殺菌消毒劑(Antiseptic
Agents)。
(6)固體添加劑(Solid
Lubricants Fillers)。
(7)消斑劑(Anti-Stain
Additives)。
(8)消音劑(Anti-Chatter,Anti-Squawk
Agents)。
圖表9.中國大陸石油添加劑的分類
類 別 |
組 號 |
組 別 |
品 名 |
編 號 |
舊編號 |
潤 滑 劑 添 加 劑 |
1 |
清淨劑和分散劑 |
102清淨劑 |
T-102 |
T-102 |
105清淨劑 |
T-105 |
- |
106清淨劑 |
T-106 |
- |
108清淨劑 |
T-108 |
T-108 |
109清淨劑 |
T-109 |
T-109 |
111清淨劑 |
T-111 |
T-111 |
151分散劑 |
T-151 |
T-113 |
152分散劑 |
T-152 |
T-113B |
153分散劑 |
T-153 |
- |
154分散劑 |
T-154 |
- |
155分散劑 |
T-155 |
- |
2 |
抗氧抗腐劑 |
201抗氧抗腐劑 |
T-201 |
T-201 |
202抗氧抗腐劑 |
T-202 |
T-202 |
203抗氧抗腐劑 |
T-203 |
T-202-2 |
3 |
極壓抗磨劑 |
301極壓抗磨劑 |
T-301 |
T-301 |
304極壓抗磨劑 |
T-304 |
T-304 |
305極壓抗磨劑 |
T-305 |
T-305 |
306極壓抗磨劑 |
T-306 |
T-306 |
321極壓抗磨劑 |
T-321 |
T-308 |
322極壓抗磨劑 |
T-322 |
T-302 |
341極壓抗磨劑 |
T-341 |
T-307 |
潤 滑 劑 添 加 劑 |
4 |
油性劑和摩擦改進劑 |
401油性劑 |
T-401 |
T-401 |
402油性劑 |
T-402 |
T-402 |
404油性劑 |
T-404 |
T-404 |
405油性劑 |
T-405 |
T-405 |
405A油性劑 |
T-405A |
- |
406油性劑 |
T-406 |
T-406 |
5 |
抗氧化劑和金屬減活劑 |
501抗氧劑 |
T-501 |
T-501 |
531抗氧劑 |
T-531 |
- |
551金屬減活劑 |
T-551 |
- |
6 |
黏度指數改進劑 |
601黏度指數改進劑 |
T-601 |
T-601 |
602黏度指數改進劑 |
T-602 |
T-602 |
603黏度指數改進劑 |
T-603 |
T-603 |
611黏度指數改進劑 |
T-611 |
T-604 |
7 |
防 銹 劑 |
701防銹劑 |
T-701 |
T-701 |
702防銹劑 |
T-702 |
T-702 |
703防銹劑 |
T-703 |
T-703 |
704防銹劑 |
T-704 |
T-704 |
705防銹劑 |
T-705 |
T-705 |
706防銹劑 |
T-706 |
T-706 |
708防銹劑 |
T-708 |
T-708 |
711防銹劑 |
T-711 |
- |
743防銹劑 |
T-743 |
T-743 |
746防銹劑 |
T-746 |
T-746 |
8 |
降凝劑 |
801降凝劑 |
T-801 |
T-801 |
803降凝劑 |
T-803 |
T-803 |
803A降凝劑 |
T-803A |
T-803A |
9 |
抗泡沫劑 |
901抗泡沫劑 |
T-901 |
T-901 |
911抗泡沫劑 |
T-911 |
T-902 |
燃 料 添 加 劑 |
11 |
抗爆劑 |
1101抗爆劑 |
T-1101 |
T-1101 |
12 |
金屬鈍化劑 |
1201金屬鈍化劑 |
T-1201 |
T-1201 |
13 |
防冰劑 |
1301防冰劑 |
T-1301 |
T-1301 |
1302防冰劑 |
T-1302 |
T-1302 |
14 |
抗氧防膠劑 |
|
|
|
15 |
抗靜電劑 |
1501抗靜電劑 |
T-1501 |
T-1501 |
16 |
抗磨劑 |
1601抗磨劑 |
T-1601 |
T-306 |
1602抗磨劑 |
T-1602 |
|
17 |
抗燒蝕劑 |
1733抗燒蝕劑 |
T-1733 |
|
18 |
流動改進劑 |
1804流動改進劑 |
T-1804 |
T-804 |
1804A流動改進劑 |
T-1804A |
|
19 |
防腐蝕劑 |
|
|
|
20 |
消煙劑 |
|
|
|
21 |
助燃劑 s |
|
|
|
22 |
十六烷值改進劑 |
|
|
|
23 |
清淨分散劑 |
|
|
|
24 |
熱安定劑 |
|
|
|
25 |
染色劑 |
|
|
|
30 |
汽油機油複合劑 |
3001QB級複合劑 |
|
|
3011QC級複合劑 |
|
|
3031QD級複合劑 |
|
|
3041QE級複合劑 |
|
|
3061QF級複合劑 |
|
|
複 合 添 加 劑 |
31 |
柴油機油複合劑 |
3101CA級複合劑 |
|
|
3121CC級複合劑 |
|
|
3141CD級複合劑 |
|
|
32 |
通用汽車發動機油複合劑 |
|
|
|
33 |
二衝程汽油機油複合劑 |
|
|
|
34 |
鐵路機車油複合劑 |
|
|
|
35 |
船用發動機油複合劑 |
3501船用汽缸油複合劑 3521船用系統油複合劑 3541中速筒狀活塞發動 機油複合劑 |
|
|
40 |
工業齒輪油複合劑 |
4001普通工業齒輪油複合劑 4021中負荷工業齒輪油複合劑 4041重負荷工業齒輪油複合劑
|
|
|
41 |
車軸齒輪油複合劑 |
4101普通車輛齒輪油複合劑 4121中負荷車輛齒輪油複合劑 4141重負荷車輛齒輪油複合劑
|
|
|
42 |
通用齒輪油複合劑 |
|
|
|
50 |
液壓油複合劑 |
5001抗氧防銹液壓油複合劑 5011抗燃液壓油複合劑 5021抗磨液壓油複合劑 5051低溫液壓油複合劑 |
|
|
60 |
工業潤滑油複合劑 |
6001汽輪機油複合劑 6021壓縮機油複合劑 6041導軌油複合劑 |
|
|
70 |
防銹油複合劑 |
|
|
|
其他 |
80 |
|
|
|
|
(六).摻配精製而成之潤滑基礎油(Lube oil base stock,或Lube stock)
精製而成之潤滑基礎油(Lube
oil base stock,或Lube
stock),按其黏度之不同分有輕質油、中質油、重質油及亮滑油(Bright
Stock)等,必須與必要添加劑摻配(Blending
and Compounding)而成特定品質之機油或製品。
所謂摻配者,乃指以不同黏度之油料彼此「摻合」(Blending),以及不同黏度之油料再混以添加劑「調配」(Compouning),而成市場上所需之特定品質潤滑油成品之總稱。
圖10表示以各種不同之潤滑原料與各種添加劑相混摻配成各種成品油之圖解。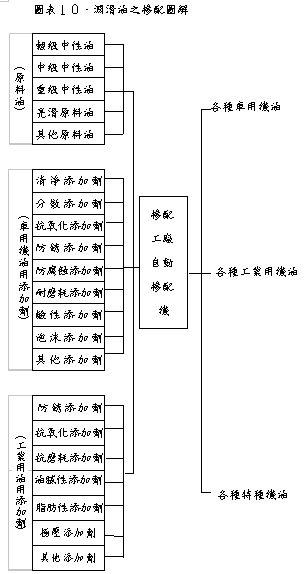
(七).包裝
潤滑油脂製妥之後,除以散裝(Bulk)方式以油罐火車、油罐汽車、油管,或油輪運往交用戶外,絕大部份之油料,都以下列方式包裝後,運往市場供售。
潤滑油之包裝
(A)200公升或53加侖鐵桶(53GallonSteel
Drums)裝--此為18號鐵皮(No.18GageSteel
Sheet)製之鐵桶,桶頂有大小口蓋各一,大口為2又
1/2英吋,小口為1/2英吋。桶面直徑大約22.5英吋(57cm),高約33.5英吋(90cm),佔7.4立方英尺之空間,重約53磅或24公斤,符合美國ICC-17E規範。
此種油桶裝滿油料時可達212公升,但包裝任何液體,不可裝滿,以免受熱膨脹而破裂。故通常都裝至:200公升(53加侖)或208公升(55加侖),(尚有2﹪之空間)。
上述之加侖乃美加侖(U.S.
Gallon,簡稱U.S.
Gal.),每一美加侖相當於3.785公升。在英國地區使用之英加侖(Imperial
Gallon,簡稱Imp.
Gal.或I.G.)相當於4.543公升(即等於62℉時清水10磅之體積,或277.27立方英吋)。
(B)18公升手提桶(5
Gallon Pails)裝--桶頂附提把手,一人兩手可各提一桶,提運方便,每桶淨裝18公升或5加侖。
(C)4或3.8
公升1加侖罐(1GallonTin)裝--淨裝
3.8
公升。
(D)1公升或1誇特(1Liter
or1 Quart Tin)裝--淨裝1公升或1誇特(0.95公升)。
(E)1000公升大批量包裝:近年來市場漸流行可重覆使用的大容量-1000公升槽,多為塑膠製品,下方裝置旋扭式出油口,方便用者分批漏出使用,槽可回收重覆利用,唯搬動時須有堆高機等機具配合。
潤滑脂之包裝
(A)181.2公斤或400磅裝--與上述200公升裝相似,但為大形頂蓋之鐵桶(Full
Open Head Drum)。
(B)15公斤或35磅手提桶(15kg
or 35 pound Pails)裝--其大小與上述19公升裝相似,但亦為大型之廣口蓋。
(C)0.45公斤或1磅罐裝。圖表11.潤滑油.脂常見包裝
|